Tucked into the basement of the University of Iowa’s Seamans Center is the Engineering Machine Shop, a high-tech workshop where students provide consulting, design, prototyping, and fabrication services to faculty, staff, and peers at the UI.
The shop provides hands-on experience for student workers, most of whom are mechanical engineering majors, and university clients, such as faculty researchers, benefit from having a full-service shop on campus.
Led by manager Steve Struckman and staff engineer Bill Jennings, the students learn how to safely operate machinery, including lathes, mills, saws, 3–D prototyping equipment, and hand tools to complete projects for classes and clients. Struckman, who became manager in 2010, started working at the machine shop in 1996. Read on for some of his favorite projects of the past 20 years:
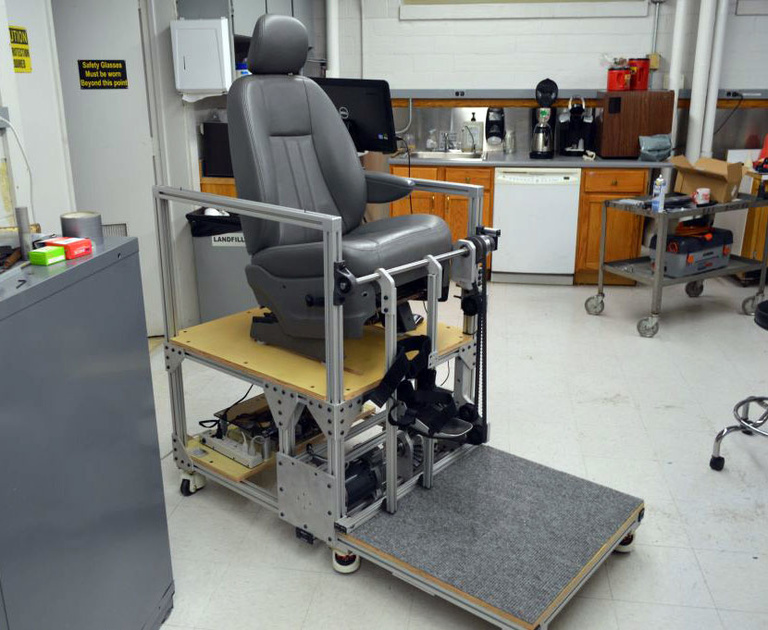
1. Leg ergometer: Working with physical therapy researchers, machine-shop staff built a leg-kicking device that helped the researchers gain access to a subject's femoral artery while providing a resistive force that the subject could actively oppose. The one-leg ergometer allowed researchers to simultaneously measure the amount of work done by the quadriceps and create ultrasound images of the artery during the movement.
2. Air samplers: At the request of College of Engineering Associate Dean Keri Hornbuckle, machine-shop staff built air-sampling devices that could detect polychlorinated biphenyls—PCBs. The devices were mounted on motor homes that researchers drove to different schools throughout Chicago to attend to elementary school students experiencing asthma problems. At each school, the vacuum-like devices filtered the local air and sent samples back to the UI for evaluation.
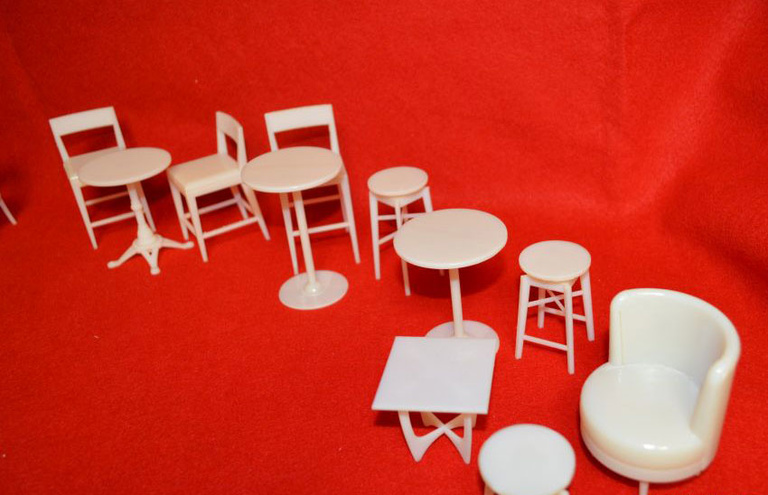
3. Tiny furniture: An industrial designer at Starbucks whose father used to work at the machine shop recently contracted the UI to build tiny model furniture to help launch new kiosk stores in India. Struckman says local furniture makers in India couldn’t read blueprints, so Starbucks instead used the machine shop’s two- to three-inch models as guides.
4. Artificial ankle joints: A group of senior biomedical engineering students contacted the machine shop to build artificial ankle joints for a class project. The external prosthetic limbs were meant to help people in the developing world, such as those with below-the-knee leg amputations.
5. Auto transmission: Struckman says one of the shop's most frequent clients is the UI's Society of Automotive Engineers. In addition to building smaller car parts that society members can't make themselves, he says the most complicated order they completed was an automotive transmission.
Do you have a project for the machine shop? Stop by the shop at G450 SC to discuss your idea.